Future packing robots exploit collisions, instead of fearing them
With the rise of e-commerce, robots have become indispensable in distribution centers across the world. However, logistics robots are not as smart and fast as you might think. TU/e, together with several partners, has started a four-year research project focused on impact-aware robot manipulation in the logistics domain. The EU supports the I.AM. project with a 4.4 million euro grant.
As we all know, robots are extremely good at routine operations. You can program them to pick up objects and place them into a box or on a conveyor belt. The problem is that, because the robots cannot forecast the effect of collisions and are therefore unable to prevent possible harm, these robotics arms need to halt just before they place down or pick up a package, slowing up the whole process. In other words, current robots may be precise and reliable, but they are also quite poor at handling dynamic contact tasks. They fear impacts, instead of exploiting them.
Toss or slam
People are much better at predicting the consequence of a collision and decide if it could be harmful or not for a given object and themselves. People are therefore a lot faster at handling objects than robots. They are able to put an item on a conveyor belt in one single fast movement, even deciding to toss or slam the item onto the conveyor to speed up the process, without damage. Similar challenges occur when we want to place quickly items in a crate or a box. Not only are people faster at this than robots, they are also much better at filling the container as densely as possible, by quickly pushing objects into it.
Humans are also still the preferred option when unloading pallets, a process that is known in logistics as depalletising. Automatic systems do exist for this, but they are quite expensive and take up a very large space. Even in this context, an impact-aware robot would be a godsend, learning to predict the effect of simultaneous collisions and quickly react to unexpected impact situations via reflex actions.
Learning robots
In the I.AM. project, researchers from the TU/e, together with colleagues from Technical University of Munich, École polytechnique fédérale de Lausanne, and the Centre National de la Recherche Scientifique, will make robots able to reliably predict the effect of soft and hard collisions with surrounding objects and environment on their movements, so that they can exploit impacts to speed up and improve pick-and-place and packaging tasks.
Read on below the image.
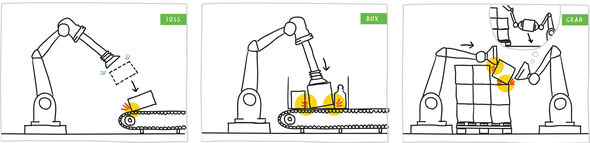
The researchers want to achieve this in a number of ways: by designing advanced models that can predict what happens when the robot, package or conveyor belt collide with each other; by using artificial intelligence so that the robot learns how to move quickly without causing damage; and by developing sensing methodologies that give the robot an advanced sense of touch so that it knows what is happening even when collisions are occurring. The new technology will be built into existing state-of-the-art soft robots so that it can be rolled out quickly. Alessandro Saccon, assistent professor at the department of Mechanical Engineering and coordinator of this EU project on behalf of TU/e, expects that this will enable these robots to work ten percent faster.
Huge potential
Saccon sees huge potential for impact-aware robotics in the logistics domain: "E-commerce is booming, and in a tight labor market it is becoming increasingly difficult to find personnel. Moreover, work in distribution centers is often repetitive, and potentially bad for your health. Impact-aware robotics can relieve employees from these routine tasks, so that they have their hands free for different work".
In the project, the researchers are working closely with four companies that specialize in logistics, automation, robot manufacturing and physics simulation: Vanderlande and Smart Robotics, both from the Netherlands, Munich-based Franka Emika, and the Swedish company Algoryx.
The project name I.AM. is an acronym that stands for Impact-Aware Manipulation. The European Union supports the project with a grant of 4.4 million euros.
Discussion