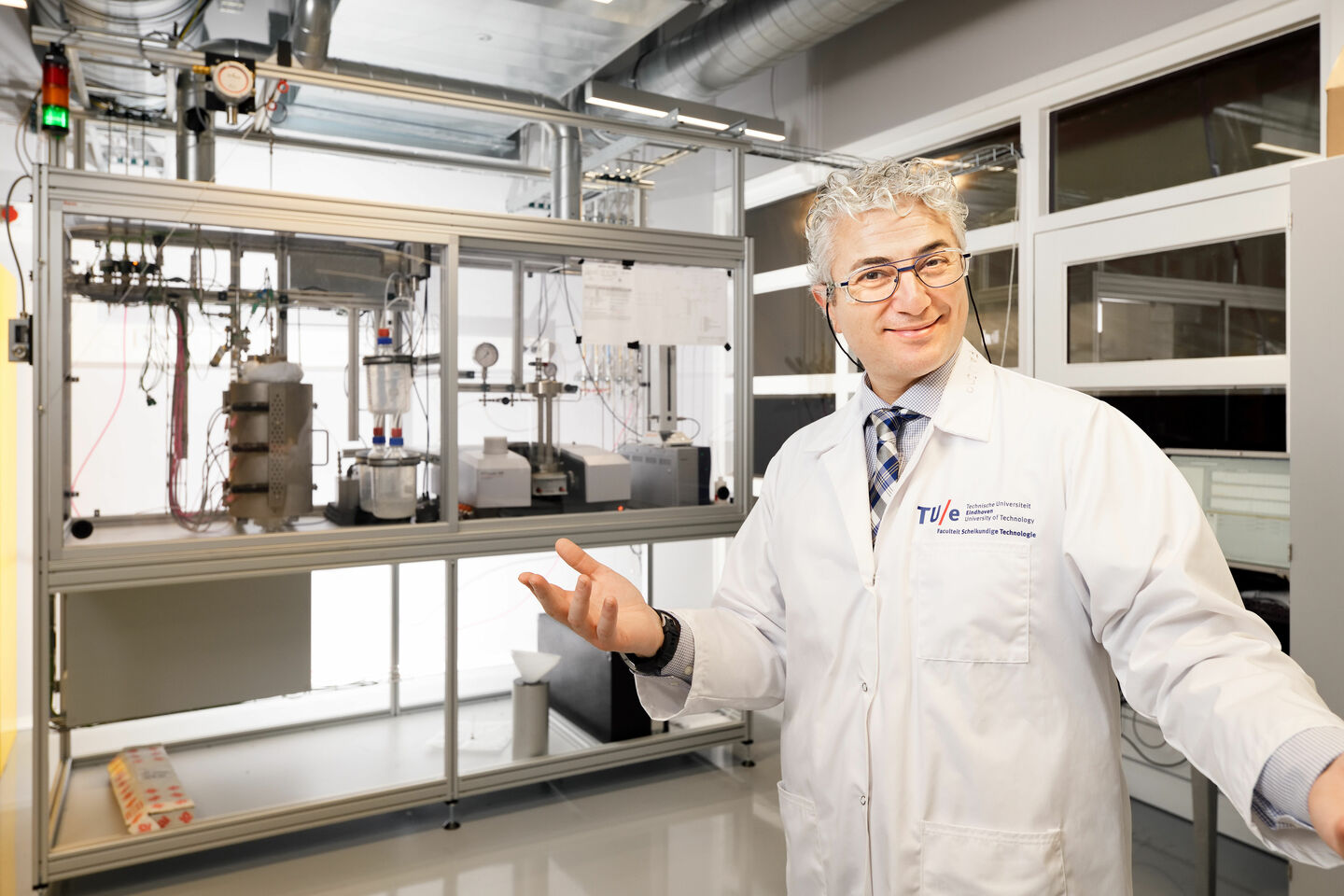
European top scorer takes smart reactors forward
Towards the end of last year process engineer Fausto Gallucci secured four European projects related to ‘smart’ chemical reactors - enough work for thirteen new doctoral candidates. This brings the Italian's count of European projects in which he participates or has been appointed scientific coordinator to an impressive twenty-two, all achieved in the scarcely ten years he has been working at TU/e. What is his secret?
Fausto Gallucci's track record in Europe was already outstanding, but gaining four new EU grants takes his score with European funding bodies to a whole new level. In the coming months his group will actually double in size. “I now have ten doctoral candidates and four postdocs,” the professor of Inorganic Membranes and Membrane Reactors says. “And no permanent staff to provide support.” So supervising all these young researchers is going to be hard work in the years ahead, he admits.
“Fortunately, together with the groups run by John van der Schaaf, Timothy Noël and Evgeny Rebrov we've taken the initiative to form a cluster of our own, Sustainable Process Engineering, within Chemical Engineering and Chemistry. Assistant Professor Fernanda Neira d’Angelo, a participant in one of my new projects, also falls within this cluster, an arrangement by which we can cooperate easily and share facilities.”
Winter school
All in all, Gallucci gets some 70 percent of his research funding from Europe, he estimates. This, he says, is due largely to his good network. “We work very closely, for example, with Spain's Tecnalia, a large private research institute. This collaboration came about during a winter school in Germany at which I was giving lectures to Spanish students.” They got talking and one thing led to another, he explains.
“Tecnalia is strong in material development, and reactor technology is our field, so we complement one another. And the personal contact is good, as it has to be. You need to be very open with each other, even to the point of readily admitting when something isn't going to work after all. We also present ourselves as one team when we're at conferences, which seems to work well.”
Another institution with which the Italian has previously collaborated in numerous projects is the Politecnico di Milano, a leading technology university in the country of his birth, and to this list we can add the University of Manchester and various companies who are interested in (aspects of) the developed technology. One project often gives rise to the next. “You ought do all you can to make the project a success. At the EU they work on the assumption that only one in ten projects will be successful, but those that are provide new technology and employment.”
Simply being able to present a project as a success makes an impression, is what he means to say. “The focus of the first EU project, ten years ago, was a piece of membrane measuring a few square centimeters but in successive projects we've managed to scale up this technology used in the production of hydrogen to create a reactor that is now about to undergo months of testing in factories in Spain and France. These forthcoming membrane projects will involve a total investment of 38 million euros.”
Calabria
Gallucci comes from Calabria, the southern province that forms the toe of Italy's 'boot'. At the local Università della Calabria he studied chemical engineering. As a master's student there he worked on a project to convert CO2 and hydrogen into methanol in a membrane reactor - “as one of the first to do so” - and later as a PhD candidate he split methanol into hydrogen and CO2. “So I was back where I started,” he jokes. “But in the meantime I'd gained my doctorate.”
Unfortunately opportunities to work as a scientist were few and far between in Italy at that time. “So once I had gained my doctorate I applied for a job in the Netherlands, with the energy research center ECN. I wasn't hired but they sent my application to the University of Twente, where I started work in 2007.” In 2010 he and a few of his colleagues transferred to TU/e and here, in 2018, he was promoted to a rank of professor.
This Italian says he feels comfortable in the world of Dutch science. “I enjoy going to Italy for family visits and vacations, but I prefer to work here. There is help available here, from Innovation Lab for example, they help you deal with the bureaucracy involved in running a research group and applying for grants. That is very welcome. It is competitive here, but that is good too. I am working with colleagues who I am proud of because they are so good at what they do.”
Smart reactors
Gallucci is developing ‘smart’ reactor technology by combining the chemical reaction with a separation step in a single device, often using membranes: thin barriers that act as a sieve by being permeable to selected substances.
The membranes the Italian uses take the form of hollow, sealed tubes made of palladium, ceramics or carbon that are ‘hung up’ in a reactor vessel. These membrane tubes are selective as to the substances they let through so, for example, hydrogen (in the case of the palladium membrane) or oxygen (the ceramic tubes) is extracted from the reaction mixture. The oxygen molecules or hydrogen molecules react with the membrane, split into individual atoms that can permeate the material, and recombine inside the tube.
Removing the reaction product from the reaction mixture causes a shift in the chemical equilibrium, and so the reaction can take place at lower temperatures, Gallucci explains. “Thus, for example, you can extract hydrogen from methane at a temperature of 500 degrees instead of at a thousand degrees. This saves a huge amount of energy.” Another example of such smart reactor technology is the use of plasma to activate methane at room temperature, with a similar energy gain. “Here on the campus we are collaborating on this with DIFFER.”
Bio-kerosene
Although his chair gives priority to his work with membranes, they are not involved in one of the new projects. Here, the partners want to produce bio-kerosene (for aircraft) and biodiesel (for ships) from the glycerol that is a byproduct of making other biofuels. “This is already possible,” Gallucci explains. “But we aim to do it with the minimum of CO2 emission; as energy efficiently as possible, in other words. And to get the best possible contact surface we'll be printing the catalyst we'll be using in 3D.”
Ammonia
The second new project involves developing ammonia as a sustainable storage medium for energy. Not unlike the students on Team FAST (who are carrying on their work as the company DENS, incidentally another of Gallucci's collaborators in a past European project) who were working on hydrogen storage in the form of formic acid, the Italian and his colleagues want to store hydrogen in ammonia. “Using electrolysis powered by sustainably generated electricity we'll release hydrogen from water. In a special reactor this hydrogen will be combined with nitrogen to produce ammonia.” Then it's just a matter of transporting the hydrogen in the form of ammonia, an easy-to-handle liquid, to the site where power is needed. “Once there, a membrane reactor, which we are also developing, can be used to release the hydrogen for use in a fuel cell.”
Center of Excellence
Gallucci's third new project has been set up to cluster the European centers of membrane technology into a single, large center of excellence, explains the Italian. “This brings together thirty-two partners, including some from industry, who together can provide every aspect of the membrane technology. A budget is available to have the newly developed membranes field tested by the industrial partners. After the five-year lifetime of the project, the center will continue on as a small company that we hope will serve as the focal point for European membrane research.”
As an early Christmas present, the chemical technologist received news just before the holidays that he can further appoint a PhD candidate on yet another project, this one within the European program Bio-Based Industry (BBI). “In this project we are developing three membrane products produced from biopolymers. These are intended to capture CO2 and use it to upgrade natural gas and biogas, and to treat combustion gases.”
Discussion