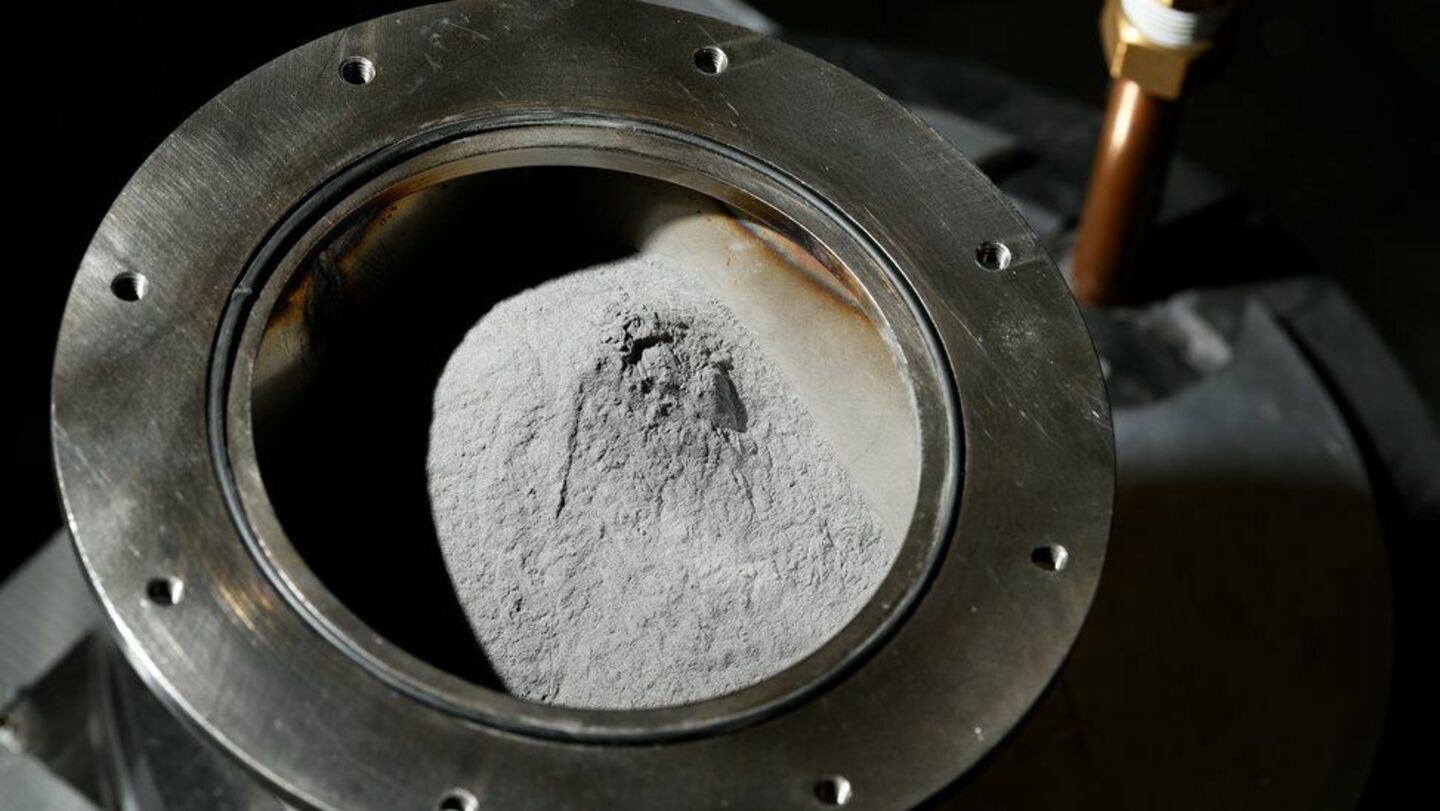
Prof Talk | Iron in the fire
Is iron powder the future of sustainable energy storage?
Ten years ago, TU/e Professor Philip de Goey took a bold step. He decided to devote the last years of his career to a new research direction: iron powder as a sustainable energy carrier. What initially seemed like a daring choice has since grown into a promising technology with the potential to accelerate energy transition.
“I really wanted to make an impact in the last years of my career,” De Goey says. That’s when he stumbled upon the idea of burning iron to release renewable energy. At the time, a research group in Canada had been researching metal combustion for years, but for very different applications, such as rocket propulsion. De Goey, however, became convinced of the use of iron powder as a storage medium for renewable energy.
He ended up making a radical choice, changing research directions and focusing entirely on iron powder for the last decade of his academic career. His goal? To fundamentally understand iron powder combustion and reduction so that this technology becomes scalable and commercially viable.
Cyclical process
The technology behind iron powder is based on a cyclical process that consists of two steps: combustion and reduction. Combustion involves a chemical reaction in which the iron reacts with oxygen from the air. This process produces a large amount of energy and results in the formation of iron oxide, a compound of iron and oxygen. As powdered iron has very fine particles, combustion is rapid. De Goey explains: “The unique thing about this process is that no CO2 or other harmful substances are released. The only thing you’re left with – besides a large amount of heat that you can use for industrial processes and other purposes – is rust, which can be collected and reused.”
After combustion, the iron oxide remains, but there’s more to the story. A second step, reduction, converts this iron oxide to pure iron. This is done by removing the oxygen that has bonded to the iron. To this end, a reducing agent – such as hydrogen – is used, which reacts with the oxygen and returns the iron to its original form. “In principle, the process is entirely circular,” De Goey emphasizes. “This means you can repeat it endlessly, as long as you create the right conditions.”
At first, people thought the idea was absurd. Burning metal and using it as an energy carrier? That would never work
Unique qualities
What makes iron powder so special? De Goey picks up a jar of the fine-grained powder and explains: “Iron powder can burn at temperatures of about two thousand degrees without evaporating. In the process, the particles remain large enough to be recaptured, which is crucial for a cyclic process.” Moreover, iron is abundant, relatively cheap, and safer to transport and easier to store than, say, hydrogen. And its energy density is much higher than hydrogen, meaning it can store much more energy per unit of volume.
Having said that, the road to success was anything but easy. “At first, people thought the idea was absurd. Burning metal and using it as an energy carrier? That would never work,” recalls De Goey. Despite iron powder’s unique properties, there were major technical challenges that initially needed to be met.
Pure combustion
The idea of burning metals isn’t new. More than a thousand years ago, the Chinese already discovered that you can burn metals to release energy and create sparks. This insight eventually led to the invention of fireworks. The real challenge lies in controlling this process so that metals burn cleanly and efficiently. “Clean combustion means that all iron particles react completely with oxygen, with no undesirable byproducts,” he explains.
Another sticking point was capturing the particles without losing any, to ensure a fully cyclic process. “You have to burn iron at the right temperature and in the right way, ensuring that it melts, but doesn’t evaporate, and that the particles remain large enough to be recaptured. With nanoparticles, that doesn’t work,” he explains.
Flame stability was also a concern. “Iron doesn’t burn as well as natural gas, so it takes some effort to keep it burning,” he says. “In the lab, we demonstrated that the system can be designed to keep the fire stable.”
There are still plenty of aspects that can be optimized, but that goes for any technology. After all, a new iPhone is also always better than the previous version
Ready for the future
An optimal solution has been found for most of the challenges, meaning the entire process is now largely under control, says De Goey. By working precisely and running the entire process under controlled conditions, one of his PhD students managed to complete ten cycles in which the iron barely changed. “We have shown that the cyclical process works,” he said.
Of course, there are challenges that remain, De Goey acknowledges. For one thing, the particles can clump together at higher temperatures, which is undesirable. In addition, his research group is studying how to speed up the reduction step, since it currently takes considerably longer than combustion. “There are still plenty of aspects that can be optimized, but that goes for any technology,” he says. “After all, a new iPhone is also always better than the previous version.”
Still, according to him, the technology is already advanced enough to be widely applied. “The fact that investors are willing to put money into start-ups working with this technology – as was recently the case with the start-up RIFT – shows that there’s sufficient confidence and that the technology is ready for the future,” says De Goey.
.
Green hydrogen
A common question is how iron powder compares to hydrogen as an energy carrier. “They aren’t competitors,” De Goey argues. “Rather, they can complement and reinforce each other.” Hydrogen plays a crucial role in the process because it’s an excellent reducing agent for iron oxide. Together, the two make a powerful duo for energy storage and transport. “Hydrogen is difficult to transport and store, but with iron you can capture that energy in a stable, solid form,” he explains.
The environmental impact of iron powder technology is highly dependent on how the reduction of iron oxide takes place. Although burning iron powder itself doesn’t emit CO2, much of the environmental benefit is lost if fossil fuels are used for the reduction. “It’s therefore essential that the reduction be powered by renewable energy, such as solar or wind power,” De Goey emphasizes.
This is where green hydrogen comes in as a key component. In countries such as Australia, where solar energy is abundant and cheap, green hydrogen can be produced at low cost. This hydrogen can then be used to reduce iron oxide to iron powder, thereby locally converting renewable energy to a stable and easily transportable energy carrier. “After reduction, you can transport the iron powder by ship to Rotterdam and from there to the industry that needs it,” De Goey says. “There you can burn it, recapture the released iron oxide, and send it back for reduction. You can theoretically repeat that process endlessly.”
Importing iron powder produced with green hydrogen is a smart way to meet our energy needs and make industry more sustainable at the same time
According to De Goey, it’s inevitable that the Netherlands will remain dependent on energy imports, as our own energy needs exceed what we can generate locally. “Importing iron powder produced with green hydrogen is a smart way to meet our energy needs and make industry more sustainable at the same time.” It’s an example of how different sustainable innovations can reinforce each other and contribute to the energy transition together. De Goey does emphasize that important steps still need to be taken. “Theoretically, all of this is already possible, but it’s essential to set up an ecosystem and an international infrastructure to actually turn it into a reality, which is what we’re working hard to achieve right now.”
Start-ups and innovation
The technology relating to iron powder has now led to the creation of several promising start-ups, such as RIFT and Iron+. These companies play a key role in developing practical applications and scaling up the technology. RIFT, which grew out of the TU/e student Team Solid, has shown that the energy from burning iron powder can be used effectively, for example for heating households. Iron+ focuses on working with international partners on large-scale and efficient use of the technology in a variety of industries.
Metalot, a research and innovation campus in Budel, is also an important link between science and practice. De Goey, who combines basic scientific research with his role as founder and board chairman of Metalot, works to bridge the gap between theory and industrial application. “At Metalot, we connect academia and industry, enabling us to take steps faster,” he explains. “This has led to the creation of the first start-ups, already ten worldwide, which are all connected to us.” In addition, De Goey has already secured several grants including the prestigious ERC Advanced Grant and an ERC Proof of Concept Grant, which stimulates the growth of the research group and the further development of the technology.
Future prospect
De Goey is optimistic about the future of iron powder. “The energy transition requires innovative solutions and iron powder can play an important role in this respect,” he says. He does emphasize that there are still challenges to overcome in the areas of innovation, scale-up, and collaboration. The success of the technology depends not only on technical breakthroughs, but also on a strong ecosystem in which science, industry, and policy come together. We also need to ensure that the technology is embraced as a solution to problems in our society. “If we continue to take the right steps, we can really make a difference,” he concludes.
Discussion