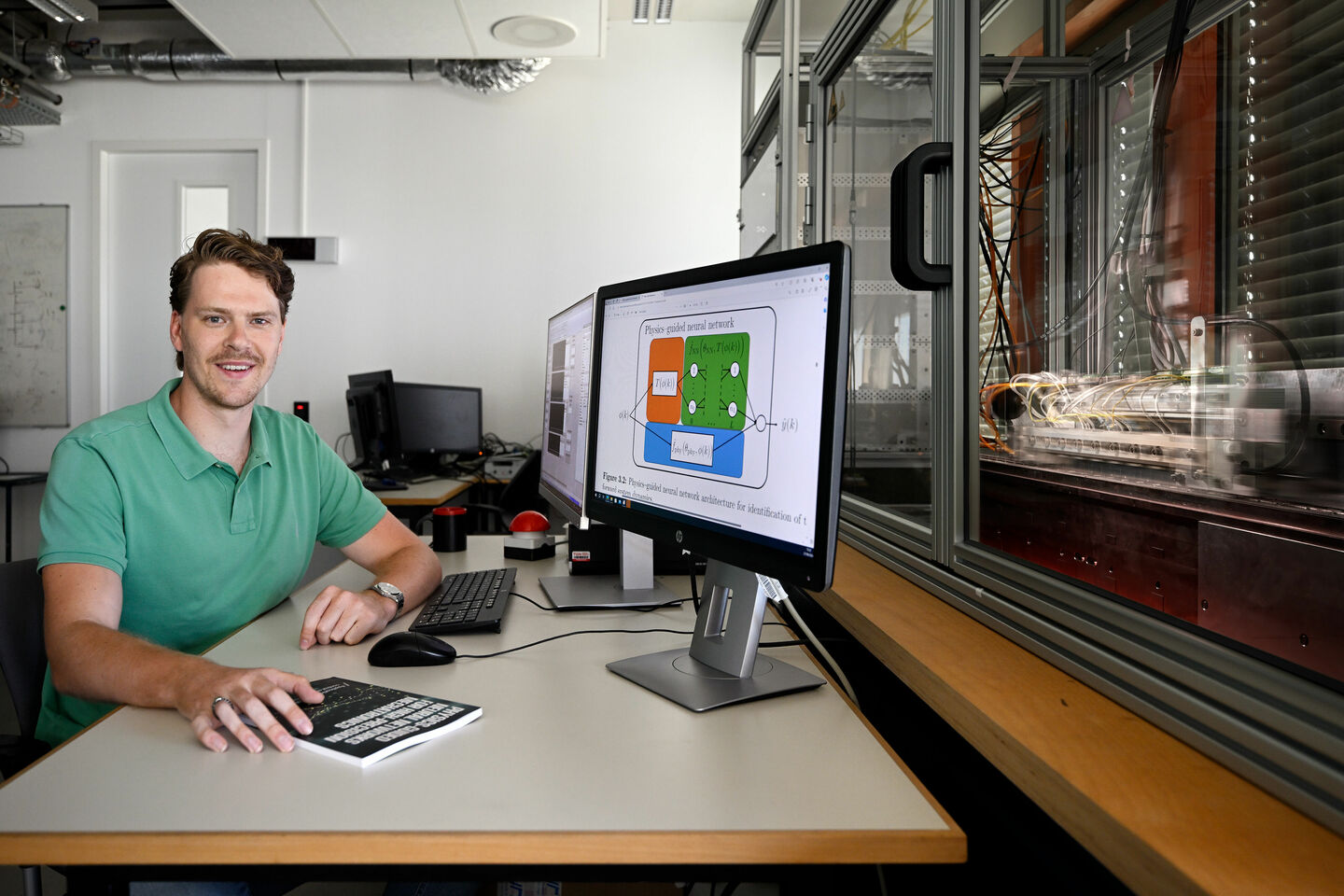
Home Stretch | Better control thanks to neural networks
PhD candidate Max Bolderman used neural networks to create a more accurate model for feedforward control
Physics-based models are used to improve the performance of, for example, ASML’s lithography machines. These models are robust and reliable, but unfortunately, they are not accurate enough. By integrating neural networks into these traditional models, PhD candidate Max Bolderman created a more accurate model that achieves better performance. Last week, he defended his dissertation at the Department of Electrical Engineering.
Bolderman carried out his research in the field of control engineering, which focuses on controlling and optimizing the performance of technical systems and processes. “Basically, control engineering ensures that the system does what you want it to do,” says Bolderman. One of the most basic examples is cruise control in cars, but the systems can range from 3D printers to autonomous vehicles, and from drones to spaceships.
In his thesis, Bolderman focused on applications in the high-tech industry of the Brainport region. For example, control technology plays a crucial role in accurately directing the movements in ASML’s lithography machines. The silicon wafers must be positioned with extreme precision so that lasers can imprint the very detailed patterns of computer chips onto them.
Feedforward control
One of the key concepts in control engineering is so-called “feedforward control”. Every system has one or more inputs and outputs, Bolderman explains. The input is what you can control, such as mechanical forces or the current. The output is often the position you want to achieve. “The question is how to choose the input to arrive at the desired output – that’s the control you have over the process,” he says. Traditionally, mathematical models are used to describe what the system does, showing how a given input influences the resulting output.
“That way, we can work backward and calculate what the input should have been to get a certain output,” he continues. But in practice, the actual system behaves somewhat differently from what the model describes. “It’s roughly correct, but not accurate enough,” argues the PhD candidate. “The physics-based models are very good for describing the basics of what happens, how the system operates in general, but they lack certain things, such as the unwanted, so-called parasitic effects such as friction.”
Neural networks
Another way to control these processes is through neural networks. “Those are black box methods that create a model of what the system looks like based on a large amount of data generated by the system,” he explains. In theory, these models can produce very accurate results, but they’re not always reliable. “It very much depends on the quality of the data,” says Bolderman. “So in general, it can work well, but you never really know. And the results are not interpretable, so that can be risky.”
To combine the best of both methods, Bolderman integrated neural networks with traditional physics-based models. That should result in models that are both more accurate and more reliable. “If you only use a neural network without providing any physical information, you end up with errors such as friction working with you instead of against you,” he says. By combining physics with neural networks, the models become more reliable. “A major advantage of these models is that you’re much less dependent on the neural networks, and thus your data. This is because you already get a lot of information from your knowledge of the mechanics,” says Bolderman. In addition, the results are more interpretable. “For example, we can now have the neural network calculate only the friction instead of the entire dynamics. That way, we can see exactly what the neural network is doing and better validate the model.”
Better performance
Bolderman’s research showed that using these models in feedforward control achieves better performance. “The system works more effectively and the position control is more accurate,” said the PhD candidate. This significant improvement in the system would allow manufacturers to make more complex chips or speed up the system to produce more chips in the same amount of time. “The errors increase at higher speed, but with a more accurate model, they stay within the margin,” he explains. “So it comes down to which advantage you consider most important. You can also make the system both a little faster and a little more accurate.”
Another possible application he mentions is in the complex medical devices that Philips makes. “If you optimize your control, you might be able to take medical pictures with higher accuracy, resulting in better diagnosis.” There are many different possible applications, but ultimately, it comes down to the same principle: by combining physics with neural networks, you can create more accurate models and gain better control of the system.
What is on the cover of your dissertation?
“Those little balls linked together resemble a neural network. Everything is connected in a wave-like pattern; this references the models we used in our research to predict friction as accurately as possible.”
You’re at a birthday party. How do you explain your research in one sentence?
“I’m working on identifying very accurate data-based models that you can then use to make the system do what you want it to do.”
How do you blow off steam outside of your research?
“Through sports. I completed a quarter triathlon last weekend; I also really enjoy mountain biking and playing soccer.”
What advice would you have liked to receive when you started your PhD?
“I’ve always been told that it’s very important to have a good relationship with your supervisor(s). You can quickly find yourself isolated in such a project and your supervisors are the only ones who know what you’re working on, so it's important to maintain good contact with them.”
What is your next chapter?
“That’s still open – I will stay with TU/e for another three months at least – but I think I’ll start working in industry. I really enjoy doing research, but I’d like to take that step into practice and get to apply the knowledge I’ve acquired.”
Discussion